Building a deck is a full-featured construction project. Most communities have restrictions for the height of decks and require stairways and railings to minimize the possibility of falls.
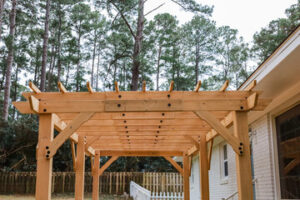
Before you start planning you’ll want to make sure the deck will be competitive in the expected metagame. A good way to test this is to run a theory test. For professional help, contact Deck Builders Murfreesboro.
Deck building is a full-featured construction project that requires a lot of tools and a substantial investment in materials. Before you decide to tackle this project, make sure you’re familiar with local regulations and have a good understanding of basic carpentry. This will help you ensure that the deck is built safely and to code. Also, check with your local authority to see if they have setbacks for decks and if permits are required.
The first step in deck building is determining the type of materials to use. There are six common options, each with its own advantages and pitfalls. The cost, maintenance requirements, expected longevity, rot and insect resistance, and aesthetics are all important considerations.
When it comes to wood, cedar is a popular choice because of its rich color and texture. However, it’s often two times more expensive than pressure-treated lumber. If you opt for this material, be prepared to stain it yearly or else it will turn grey and lose its beauty.
Composite wood is a great option for decking because it’s made from recycled materials and is eco-friendly. It’s also more durable than traditional wood, and it resists rot and insects. However, it doesn’t hold up well to direct sunlight and may fade over time.
Another option for decking is vinyl, which has the look and feel of real wood but doesn’t require staining. It’s a durable and water-resistant material, and it’s easy to install. However, it’s not a good choice for people with allergies to chemicals.
A deck isn’t complete without a staircase, and most people choose to build one using pre-made stairs or stair stringers. If you choose to use a pre-made staircase, it’s important to have it inspected by a professional before attempting installation. Depending on the style and size of your deck, you may want to add a handrail or other safety features.
Materials
Whether you are doing it yourself or enlisting a contractor to build your deck, determining the layout and selecting materials are the first steps in the design process. The type of materials you choose will impact the appearance and durability of your deck, as well as how well it blends with the architecture of your home. A knowledgeable contractor can guide you through the selection process to create a functional outdoor space that will fit within your budget.
Before beginning any work, make sure you are familiar with the building codes and permit requirements for your area. Many communities have set-back rules that dictate how close a deck can be to property lines, as well as height and structural support limitations. It is also important to contact your local building inspection office to find out if there are any restrictions or limitations on the design of your deck.
The deck structure will need to be supported by footings and beams, and attached to the house. The footings must be poured to ensure they reach below the winter frost line, which may require digging four feet or more depending on your region.
Once the footings are in place, a ledger board will be installed to tie the deck to the house and provide a solid connection for the joists. The joists are the horizontal framing members that support the decking surface, and they are usually made of pressure-treated lumber. Some decks have a rim joist, which is located around the perimeter of the deck and helps to strengthen it.
Decking boards are the final layer that makes up the visible surface of your deck, and they can be constructed from a variety of materials. Popular options include natural wood and composite materials that offer the look of traditional wooden decking with fewer maintenance demands.
You’ll also want to consider railing options, including a variety of styles and materials. For a safe and secure option that is durable, you can’t go wrong with railings made from aluminum or stainless steel. For a more refined and stylish choice, Riverhead Building Supply stocks Feeney CableRail components, featuring slender cables and hidden fittings that elevate your view while celebrating the natural beauty of wood.
Design
Deck building starts with careful planning, which involves considering the purpose and functionality of the structure. The design process also includes determining the size and layout of the deck to meet your space requirements. If you want to add built-in features like a hot tub or permanent seating, make sure you account for these in your initial plans. Finally, the design phase involves choosing materials to match your style and budget.
Before beginning a deck, it’s important to consult with local zoning authorities to determine whether there are any restrictions on heights or other structural supports for your new deck. Many communities have set-back rules that dictate how close you can build to your property lines, as well as other restrictions on the dimensions, heights and supports for stairways and railings.
Posts are the foundation of any deck, and the type of post you choose depends on how large and sturdy you want your deck to be. Most residential decks require 4”x4” posts, while larger decks may need 6”x6” posts. Once the posts are in place, they’re attached to a ledger board that connects the deck to your house wall and ground. This board is usually located directly above a buried pressure-treated footing, though it’s sometimes placed over a concrete block pier. The ledger board and posts are then used as a starting point to construct the actual frame of the deck.
During the framing phase, contractors will install interior joists and rim joists. The joists are typically spaced 12” or 16” apart and are connected at the ends to each other with metal joist hangers. Depending on your deck construction plan, the rim joists will either rest on the ledger board or be secured to it with perpendicular beams.
Another important part of the deck frame is joist blocking, which consists of blocks that are installed between each joist. This helps to distribute the weight of the deck evenly, reduces deflection (how much the joists dip under load), and makes the deck feel stiff and strong.
Once the framing is complete, a deck builder can begin installing stairs and railings. Stairs are usually made from a series of stair treads and risers, while the railing is comprised of balusters or pickets that are screwed to the deck frame. Some railing systems are a single piece of low-maintenance exterior cladding, while others use an aluminum or vinyl sleeve that wraps around the posts.
Installation
When a deck is built correctly, it adds living space and value to your home. However, even a simple deck requires careful planning and execution at every step. This includes clearing the area of any vegetation and ensuring that the ground is level to prevent structural problems later on. It’s also important to check with your local building inspection offices to determine whether there are any restrictions or permit requirements. Many communities have set-back rules that govern how close you can build to property lines, as well as specifications for heights and dimensions of the railing and stairways.
After all the plans are drawn and materials are selected, it’s time to begin construction. First, a contractor must prepare the deck site. This involves digging holes for the deck posts and removing any grass or other plants that might be in the way. The holes should be dug down to the frost line, as water that freezes in the soil can cause posts to be pushed up over time. Once the holes are dug, the contractor must pour concrete in them to ensure that they’re strong enough.
The next steps involve the installation of a ledger board, which is what the rest of the deck will attach to. This is usually a 2 x 10 or 2 x 12 board. It’s important to remove any siding that remains above the deck, and to install waterproof flashing on the side of the house. Then, the deck joists can be attached to the ledger board and the support beams that are anchored to the posts.
Now that the frame is in place, it’s time to add the details that will make your deck feel like a true part of your home. This can include utilities such as lighting options, as well as rugs and other accessories to create an inviting atmosphere. Finally, a high-quality sealant will protect the deck from moisture and keep it looking beautiful for years to come.
Choosing the right contractor for your deck build is crucial, as they’ll be responsible for executing all of these details to ensure that your new outdoor living space is both safe and aesthetically pleasing.